Aerospace Industry Applications of Honeycomb Brazing
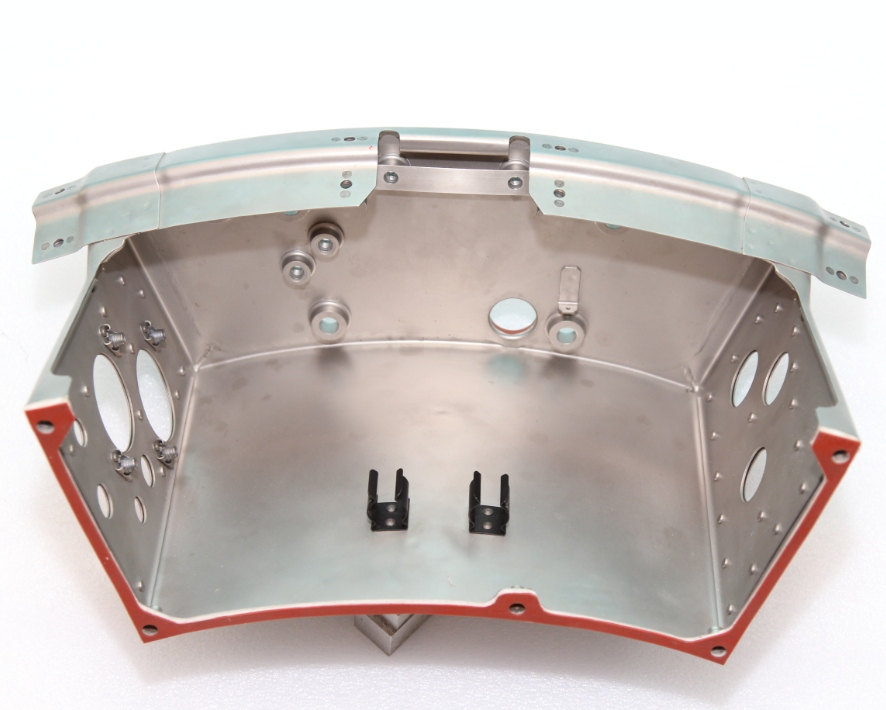
The term “honeycomb brazing” is ubiquitous in the aviation industry. If you have anything remotely to do with it, you must have heard of it at some point. What do you know about it? What is it all about exactly?
Honeycomb brazing can be thought of as a technique for crafting aeroplane parts. It is like putting together tiny, strong honeycomb shapes to make components that are tough and, at the same time, lightweight. These honeycomb structures are eminent because they are super strong and, at the same time, really light.
This article explores how honeycomb brazing works and why it is so essential for improving aeroplanes and making them better. If you are curious about all this, read on until the end.
Understanding Honeycomb Structures
Honeycomb structures get their name from their resemblance to honeycomb cells, with hexagonal shapes. These structures comprise interconnected hexagonal cells, forming a sturdy yet lightweight lattice. Their big advantage? They offer a lot of strength without adding much weight. That’s one factor which is very important in aerospace.
The Manufacturing Process: Honeycomb Brazing
Combining honeycomb structures, also known as honeycomb brazing, is a unique technique for joining them for aerospace parts. The process involves using a metal alloy, which melts at a lower temperature than the materials being joined. The alloy flows into the joints, making strong connections through capillary action, ensuring a solid bond between the parts and creating durable aerospace components.
The honeycomb brazing process can be divided into several key steps.
1. Preparation: First and foremost, the parts that need to be joined are carefully cleaned and prepared to ensure they stick together perfectly.
2. Assembly: These clean parts are put together correctly, forming the shape we want, using the honeycomb structure as a base.
3. Brazing: Everything is heated until the brazing material melts, eventually flowing into the joints, sticking the parts together well.
4. Cooling and Finishing: We let everything cool down slowly after brazing. It is possible to do extra things like shaping or treating the surface to make it look nice.
Applications of Honeycomb Brazing in Aerospace
The aerospace industry relies heavily on honeycomb brazing for various applications. Advantages include:
1. Structural Components: Think of honeycomb structures as tiny, strong hexagon shapes, like those in a honeycomb made by bees. The aerospace industry uses these shapes to build aeroplane parts like wings and engines. These honeycomb structures are super strong but also light, handy to help planes fly better and use less fuel.
2. Heat Exchangers: Sometimes, planes need parts like heat exchangers to help cool things down. Honeycomb brazing helps make these parts. The cooling systems ensure the aeroplane’s systems do not get too hot.
3. Radiators and Thermal Shields: Honeycomb brazing also produces radiators and thermal shields for spacecraft and satellites. These components are crucial in managing thermal loads and protecting sensitive equipment from extreme temperatures encountered in space.
4. Aerodynamic Surfaces: Honeycomb structures are integrated into aerodynamic surfaces such as winglets and control surfaces to enhance aerodynamic performance and stability. Brazing ensures secure attachment of these components, even under high-stress conditions experienced during flight.
5. Composite Panel Bonding: In fabricating composite panels used in aircraft interiors and structural components, honeycomb aerospace brazing is used to bond various layers of materials together, creating lightweight yet durable structures.
Challenges and Future Directions
While honeycomb brazing offers significant advantages, such as lightweight structures and improved strength, it also presents several challenges. These include ensuring uniform bonding and minimizing voids within the honeycomb structure. The ongoing advancements in brazing techniques and materials are actively addressing these challenges, paving the way for further innovation in aerospace manufacturing.
Looking ahead, future directions in honeycomb brazing include the development of advanced brazing alloys with tailored properties. Additionally, integrating automated brazing processes holds promise for enhancing efficiency and precision in manufacturing operations.
Ongoing research into novel honeycomb geometries and materials offers opportunities for optimizing the performance of aerospace components.
As the aerospace industry continues to evolve, overcoming these challenges and exploring innovative solutions will be pivotal in driving advancements in honeycomb brazing, ultimately shaping the future of aerospace engineering.
Conclusion
Honeycomb brazing has emerged as a cornerstone of aerospace manufacturing, enabling the production of lightweight yet robust components essential for modern aircraft and spacecraft. From structural elements to thermal management systems, the applications of honeycomb brazing in aerospace are diverse and far-reaching. As the aerospace industry continues to evolve, honeycomb brazing will remain at the forefront of innovation, driving advancements in performance, efficiency, and sustainability.